Choose your Preferred Category
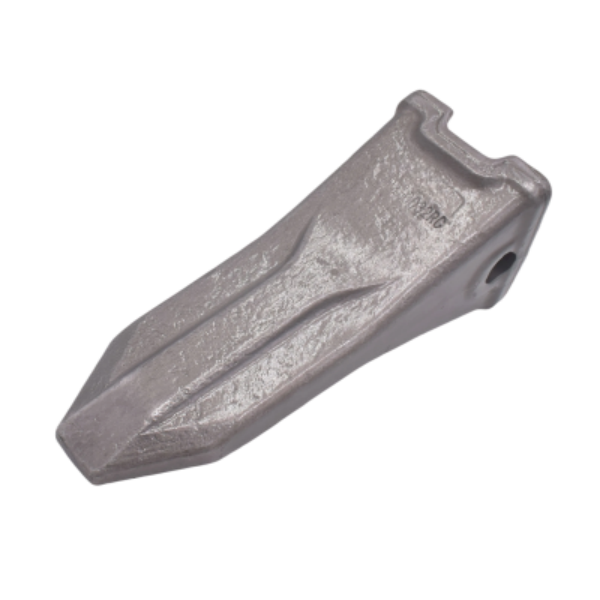
Daewoo Series
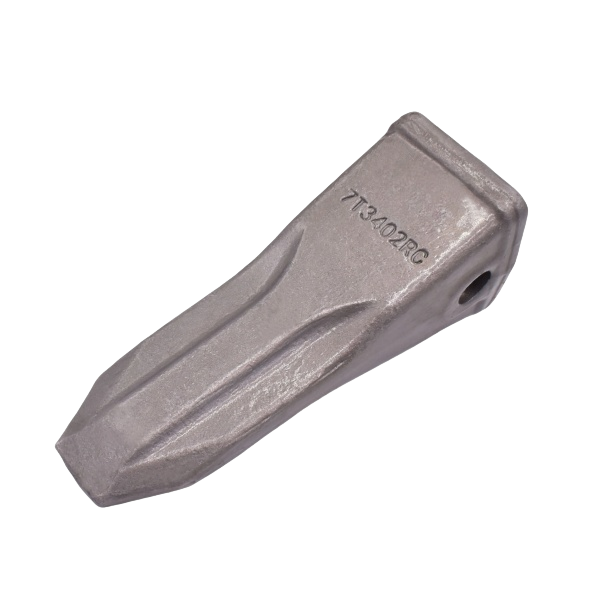
CAT Series
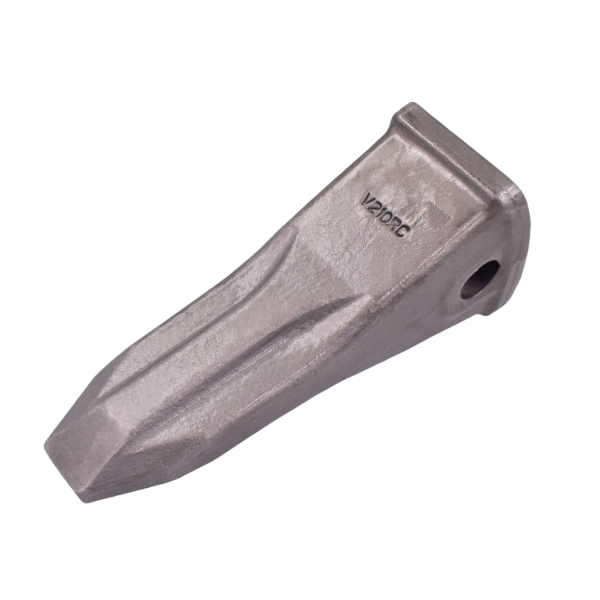
Volvo Series
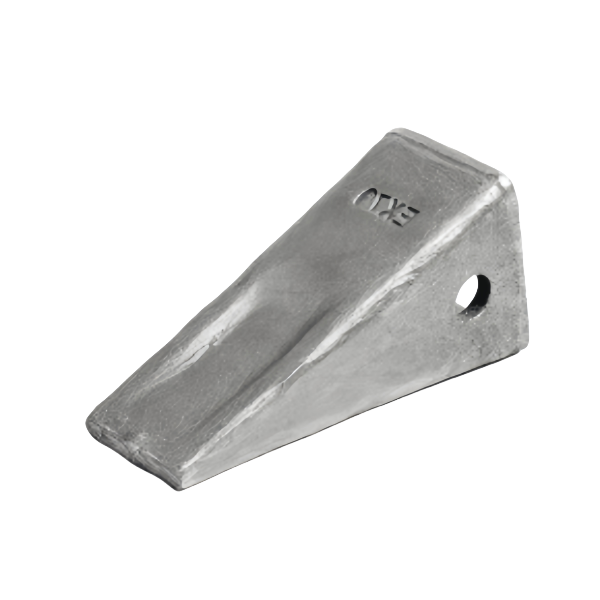
Hitachi Series
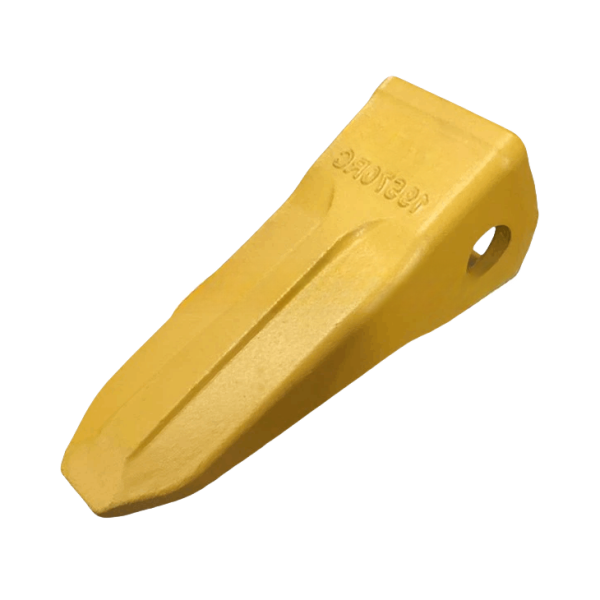
Kobelco Series
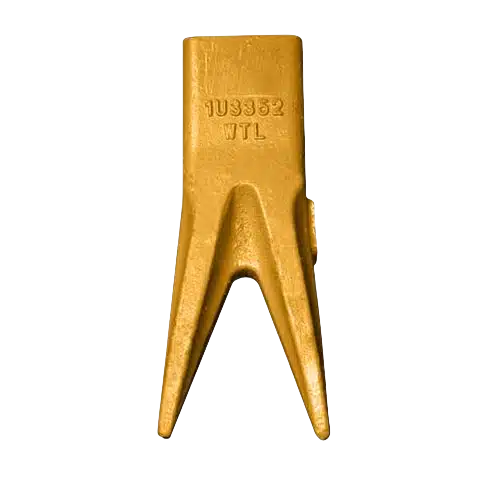
Tiger Teeth
What is the difference between forged bucket teeth and cast bucket teeth?
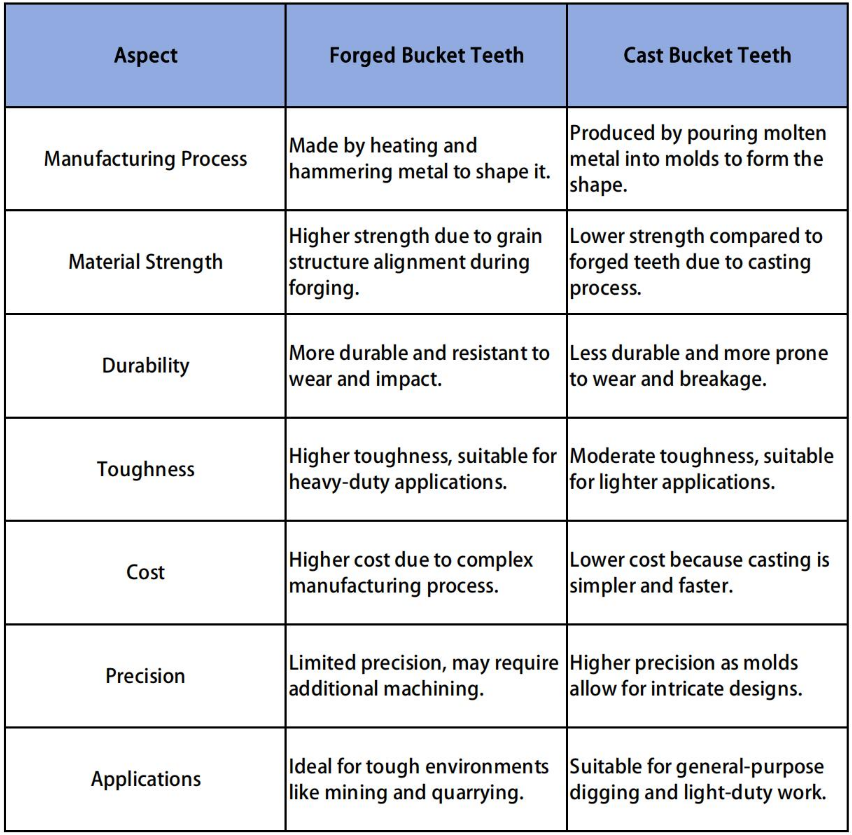
While cast bucket teeth are more economical for less demanding tasks, forged bucket teeth are the superior choice for durability,strength, and consistent performance in harsh environments.The long-term cost savings due to reduced replacementsand downtime often justify the higher initial investment in forged teeth.
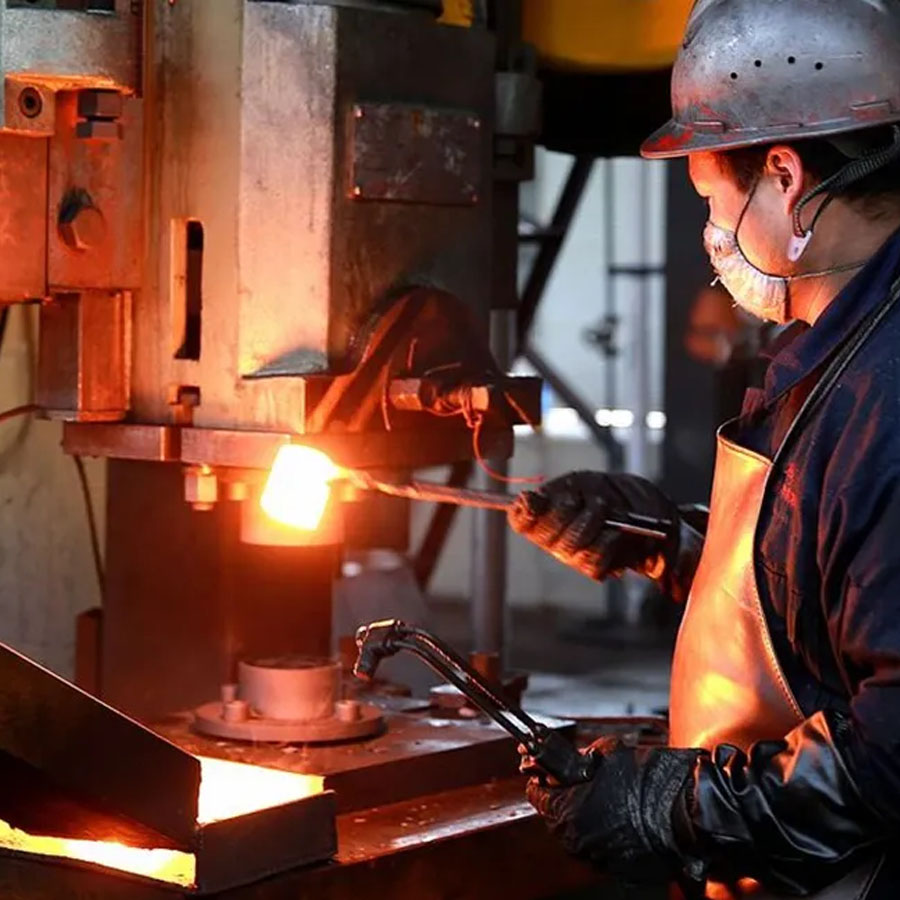
How does the wear resistance of bucket teeth affect the working efficiency of excavators?
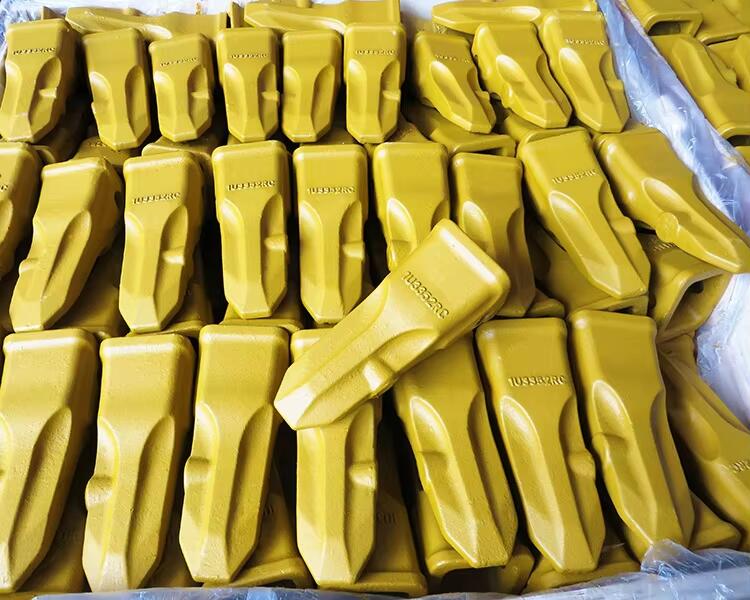
4. Adapt to different working environments
Different types of bucket teeth are suitable for different working environments. For example, rock-type bucket teeth perform well when handling hard materials, while earth-moving bucket teeth are suitable for light soil. Choosing the right high-wear-resistant bucket teeth can improve the efficiency of the excavator in specific environments and ensure optimal performance.
1. Reduce wear frequency
The bucket teeth with high wear resistance can effectively resist wear during work and extend the service life. This means the excavator does not need to replace bucket teeth for a longer period of time, reducing downtime and maintenance costs and improving overall productivity12%.
2. Improve cutting performance
Wear-resistant bucket teeth maintain a sharp cutting edge, making it easier for the excavator to cut into materials when performing earthmoving operations. When the tip portion of the bucket teeth is severely worn, the excavator needs to exert more force to complete the same work, which not only increases fuel consumption, but may also cause the equipment to be overloaded, thus affecting work efficiency13%.
3. Reduce fuel consumption
The wear resistance of bucket teeth directly affects the energy efficiency of excavation operations. Bucket teeth with high wear resistance can reduce power loss caused by wear, thereby reducing fuel consumption. Studies have shown that when the bucket teeth are severely worn, the force required by the excavator during cutting operations increases significantly, which will lead to an increase in fuel consumption and ultimately affect operating efficiency and economy.
How to choose the best bucket tooth type for you?
1. Working environment
Earthwork: For ordinary earthwork, it is recommended to use flat-head earthwork bucket teeth. This bucket tooth design can effectively reduce excavation resistance and save fuel.
Rock excavation: When facing hard rocks, RC rock bucket teeth should be selected, which have better penetration and wear resistance.
Coal seam mining: For coal seam excavation, TL pointed bucket teeth are recommended, which can improve the coal block rate.
2. Bucket tooth material
Forging and casting: Forged bucket teeth are generally more wear-resistant than cast bucket teeth, and their service life can be up to twice that of cast bucket teeth. Although forged bucket teeth are more expensive, they have better long-term economic benefits.
3. Machine model and blade thickness
Confirm the brand and model of the excavator in order to select compatible bucket teeth. At the same time, pay attention to the thickness of the blade. Blades of different thicknesses need to match the corresponding bucket tooth model.
4. Applicable working conditions
Choose the appropriate tooth tip type according to the specific working conditions. For example, for working conditions with medium wear resistance and penetration requirements, you can choose a general-purpose tooth tip; for extreme conditions, you need to choose a reinforced or specially designed tooth tip.
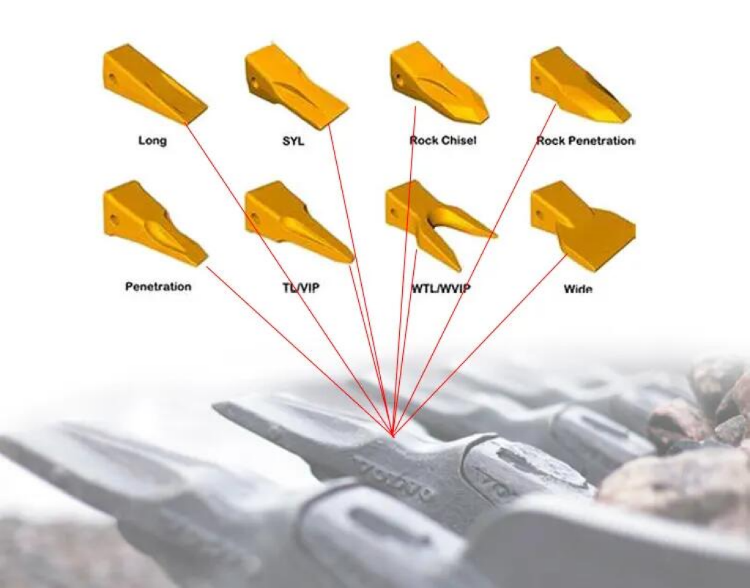
5. Maintenance and replacement
Regularly check the wear of the bucket teeth and replace the severely worn bucket teeth in time. Practice shows that the outer bucket teeth wear 30% faster than the inner ones, so it is recommended to change their positions regularly to even out the wear.
Through the above steps, you can choose the most suitable bucket tooth type according to specific operating requirements and environmental conditions, thereby improving the working efficiency and economy of the excavator.
What material are bucket teeth made of?
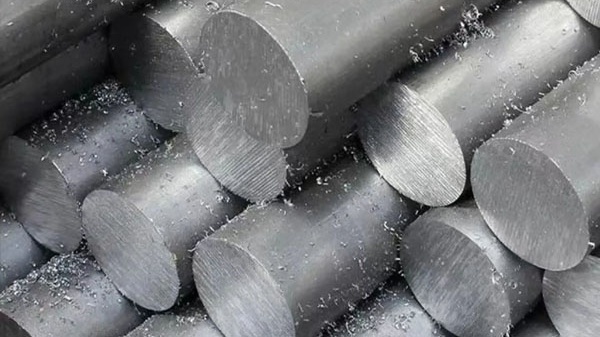
High-Quality Raw Materials
The key to a good bucket tooth is to use good steel, and select super wear-resistant round alloy steel
Is this tooth compatible with my excavator model?
Supports the following major excavator brands:
(Caterpillar)
(Komatsu)
(Hitachi)
(Doosan)
(Volvo)
(Hyundai)
(Kobelco)
Domestic brands such as XCMG, Sany, Liugong, etc.
Size standard:
Classify and match according to the bucket tooth base width, thickness, pin diameter and other dimensions. You need to confirm:
The slot size at the bottom of the bucket tooth (matching the tooth seat).
Whether the lock pin or bolt hole size is aligned.
Whether the tooth tip length and angle design are suitable for the current operation requirements
Apllications
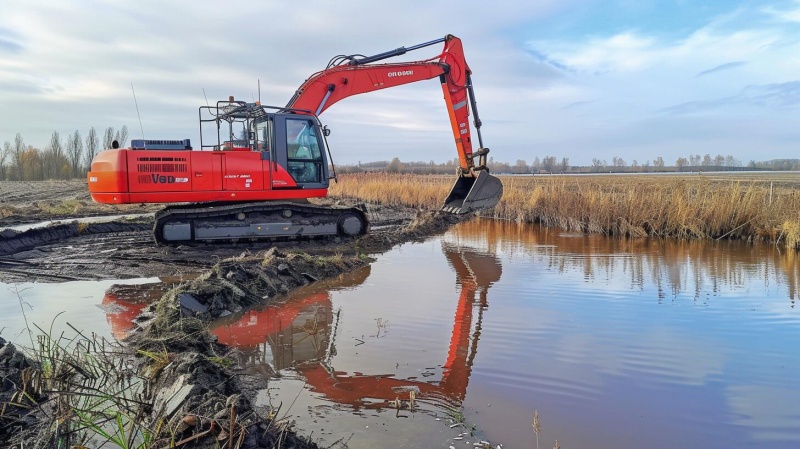
River dredging and water conservancy projects
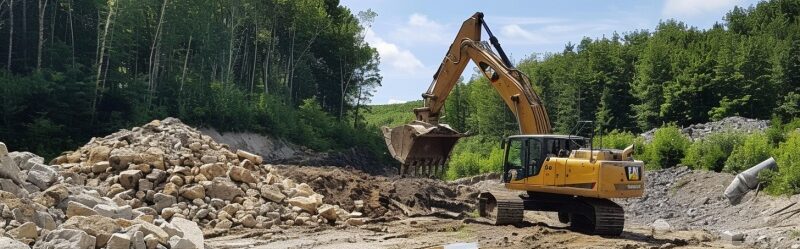
Rock Crushing and Mining
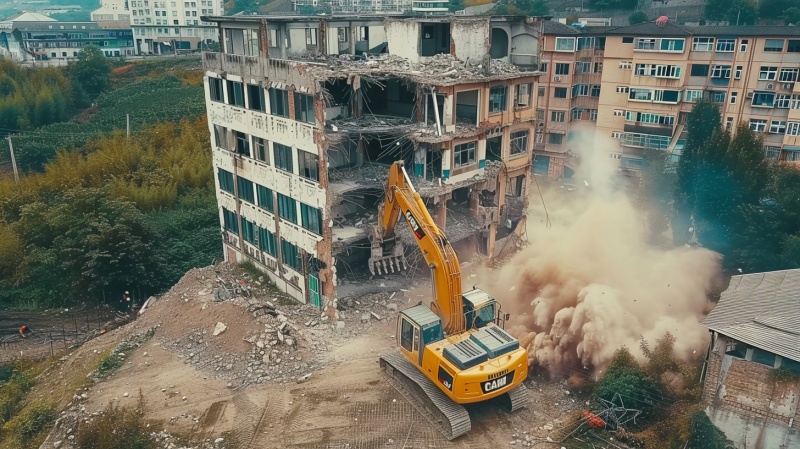
Building Demolition
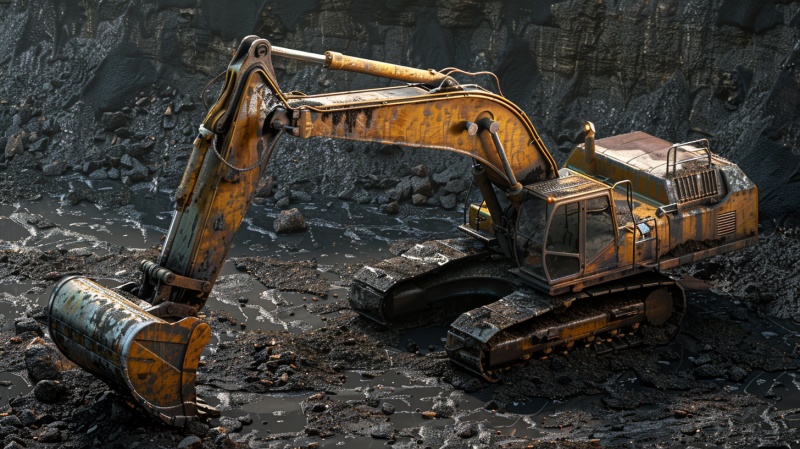
Mining operations
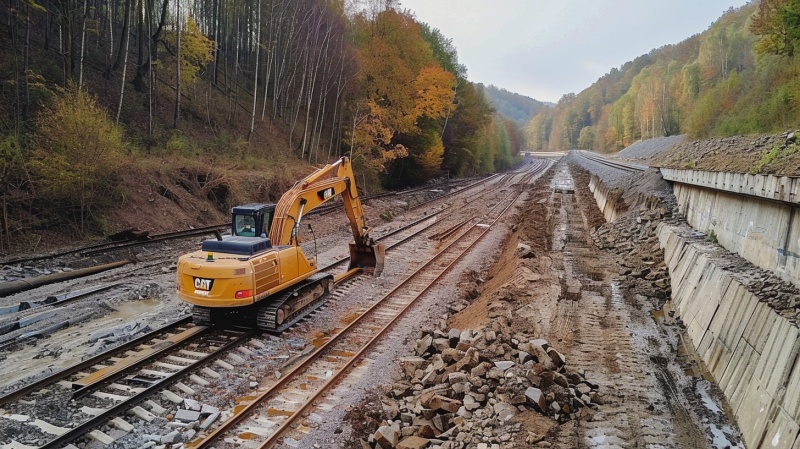
Road and railway construction
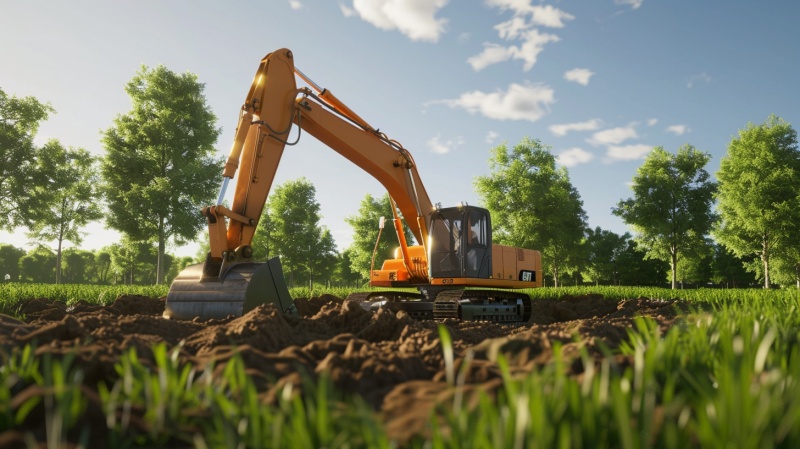
Farmland transformation
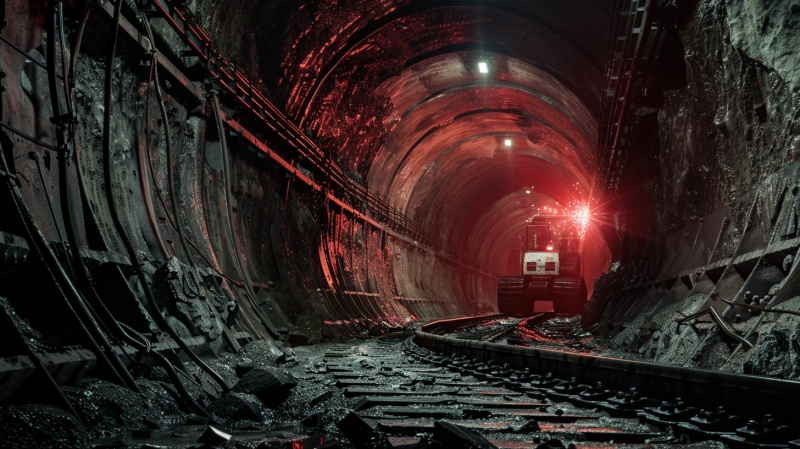
Tunnel boring
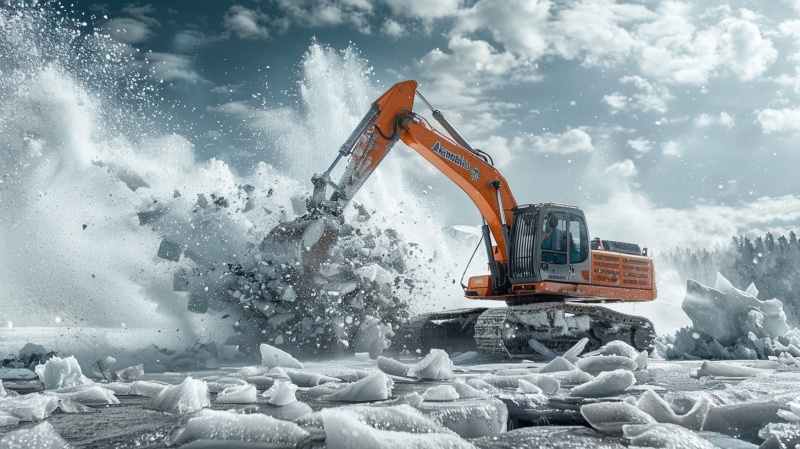
Breaking the ice
Custom Bucket Teeth With Easy
At TERA BLADE , We turn complex Into Simple! Follow the following 3 steps to start today!
Tell us what you need
Please be as specific as possible about your needs, provide pictures, tell me the brand and model you need and share your ideas.
Get solutions and quotes
We will work out the best solution according to your requirements and pictures, and a specific quotation will be provided within 24 hours.v
Approve for Mass Production
We will start mass production after getting your approval and deposit, and we will handle the shipment.